
BINDAL PLY PALACE

Bindal Ply Palace

40 +
Years of Experience

OUR BACKGROUND
It all began in the year in 1983 when our owner (Mr Anil Kumar Bindal) came to Delhi and began plywood business. In the year 1999, Bindal Ply Palace was established. The firm was established with an aim to satisfy customers with the best quality of Timber, Plywood and MDF.
Our products and services were designed to satisfy all of our customers, anytime and anywhere. We are committed to customer satisfaction as our top priority. If you want to learn more about how we do business, give us a call today.


Slide for more products
Product Range
- SYP Pine or White Pinewood
- Ivory Coast or Sagwan Teak wood
- Meranti Wood
- MDF, HDF and HDHMR
- Shera Board
- Bison Pannel Board
- Flexi Ply (6mm and 12mm)
- Pinboard and Cellotex
- Plywood and Shuttering Ply
- White Ash
- Steam Beach
- WPVC Board
- Rubberwood Board (12mm, 18mm, 25mm)
- New Zealand Pine (3 x 2 x 8 |||| 3 x 2 x 10)
- Pine MDF and Veneers

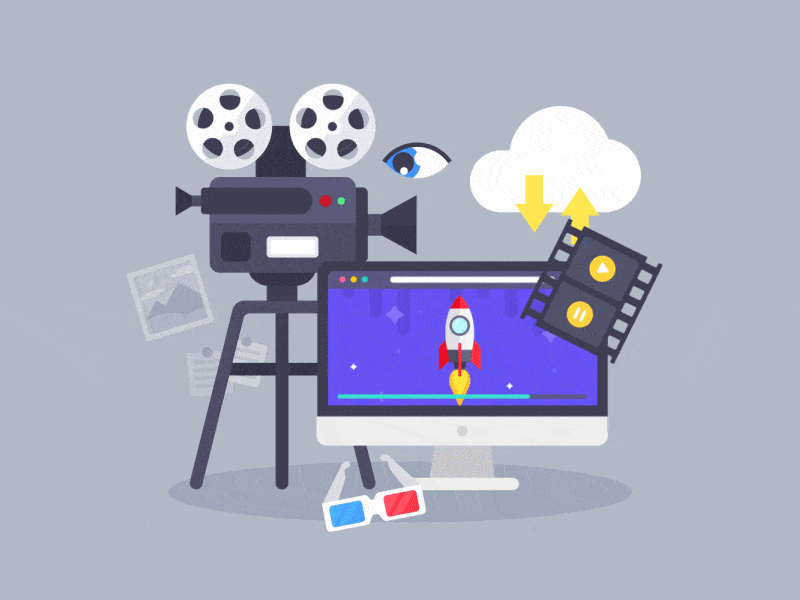
Video Gallery
CONTACT US
215/7, Rama Market, Pitam Pura, Delhi
406/1, Shop no. 2, Near Monesty, Sukhlal Market, Pitam Pura
Office Hours: Opens at 10 AM
Closes at 8 PM
E-mail ID - vireshbindal1995@gmail.com
Anil Bindal = 9810030932
011- 42696005 (Office)
Priyank Bindal = 9871751690
011- 42696205 (Office)
Viresh Bindal = 9971213025